Increase productivity.
Eliminate chaos.
"Zack teaches you the mindset to build a lean, standardized, and efficient business—powered by a culture of people working toward the same goal: getting better every day. As I tell everyone I talk to about Zack’s methods: you want this, your people want this, and your customers want this."
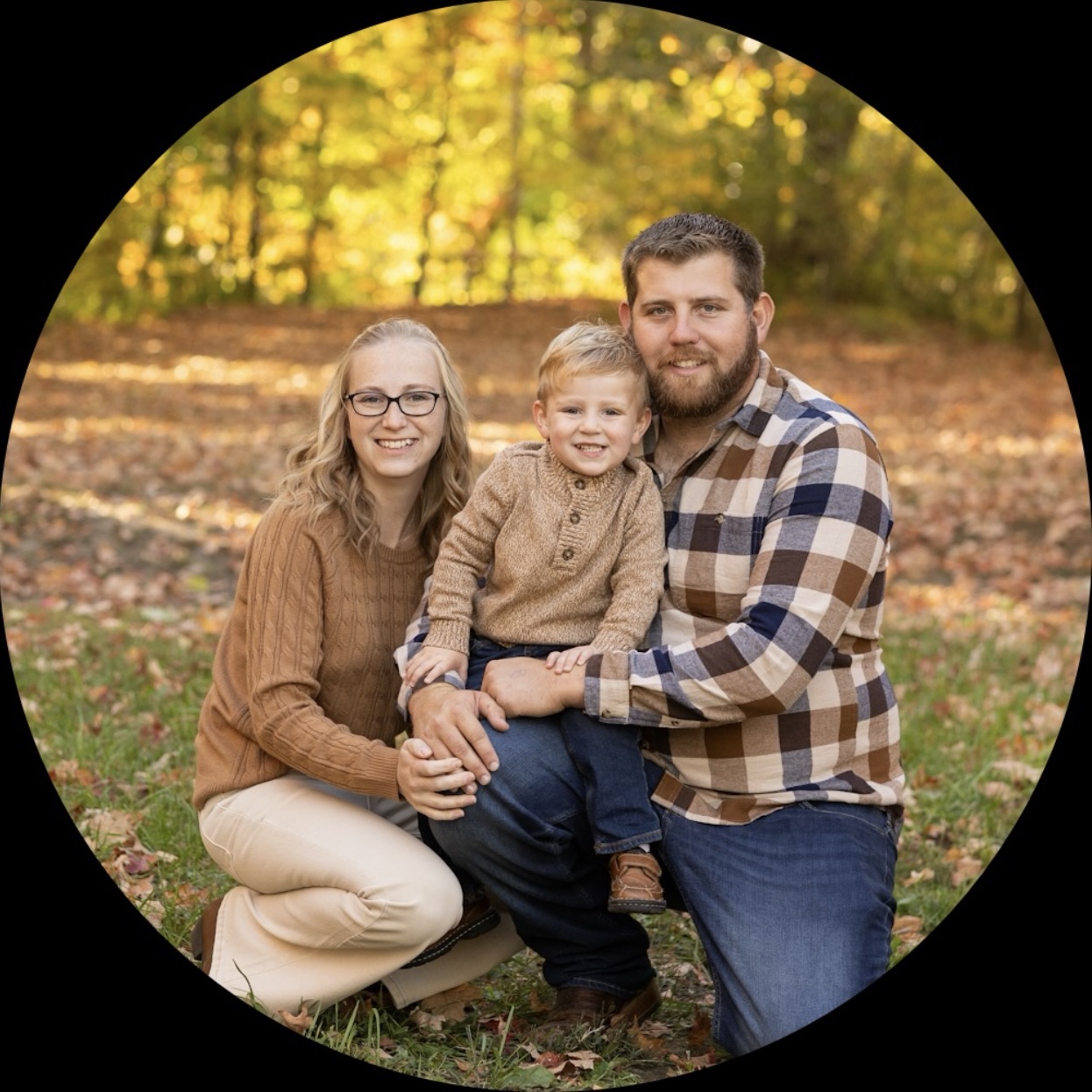
“I work with dozens of top-notch excavation contractors. I see the successes and the struggles in the industry. And I’ve watched first-hand as Zack has brought incredible value by showing my people how to create processes and systems to make their business run better (even when they’re not “systems” people).”
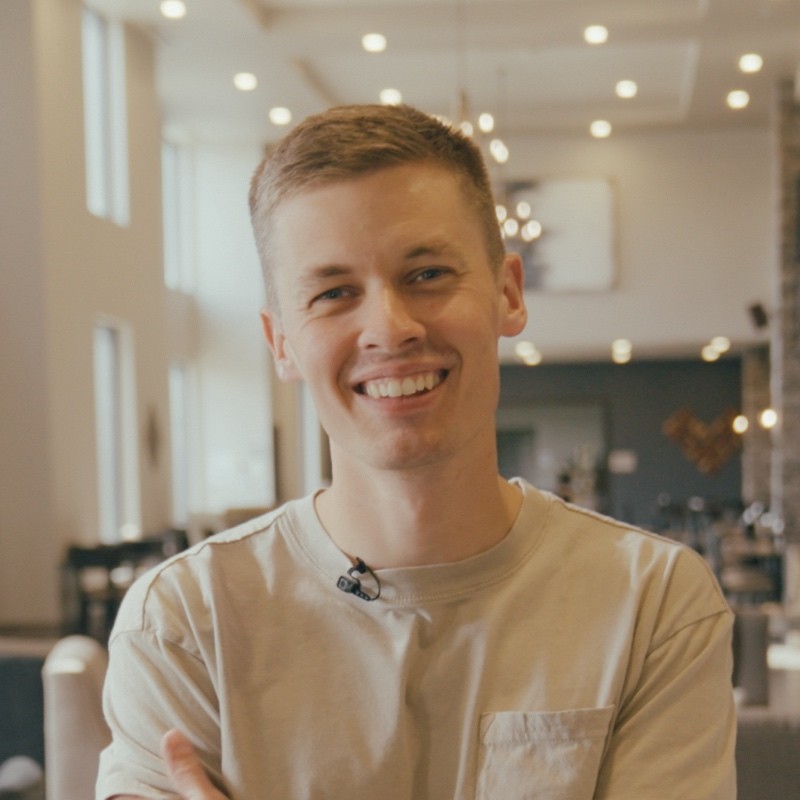
"Our company has been in business for ten years, and while some of our issues are due to geographic and seasonal challenges, our growth has stagnated due to a lack of structure and repeatable processes. This has led to difficulties in day-to-day operations due to inconsistent expectations and the limited local "head knowledge" our team members retain. Since working with Zack, we've been able to provide our team with clear expectations and our "standard way" of doing what we do. We were taught methods and tools to improve and standardize our way of doing our work and, better yet, train inexperienced team members. While sometimes it's easy to be embarrassed about the flaws that we have within our businesses, realize that Zack has seen it all. He's personable, approachable, and helpful, and wants you, your people, and your business to succeed."
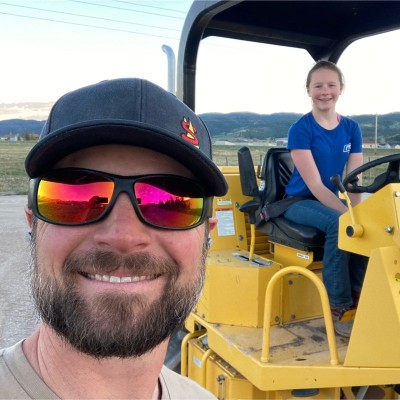
"Your skills determine your ceiling, not your circumstances."
Without
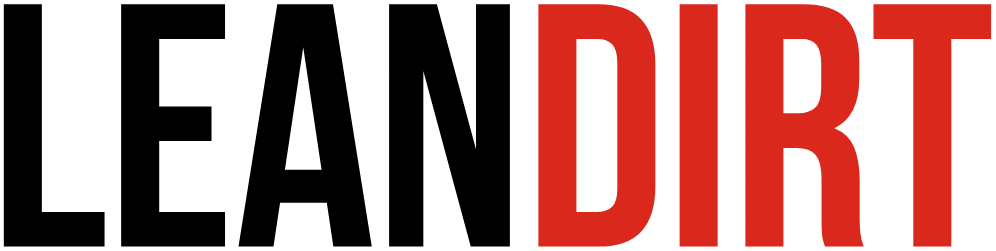
No processes
Lost knowledge
Same mistakes
Constant chaos
With
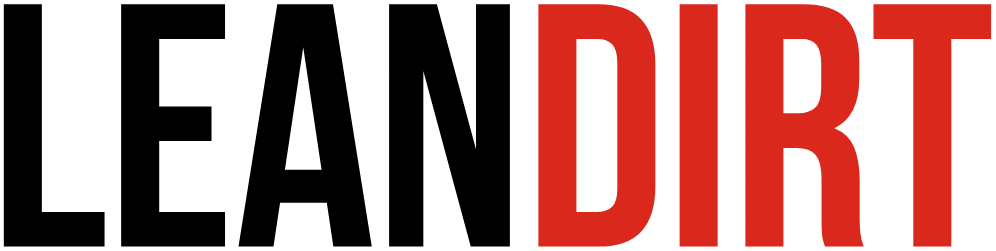
Simple systems
Documented expertise
Proactive fixes
Daily improvement
Lean Dirt isn’t just a toolkit—it’s how excellent businesses think.
We help civil contractors build lean operating systems that reduce friction, capture what works, and make continuous improvement part of the culture.
Because when your crew knows the right way to work—and has the tools to do it—it shows in your bottom line.
How It Works: 3 Components
Who am I?
Hey, I’m Zack Estes. I come from manufacturing, where process is everything.
But at a conference on manufacturing operational excellence, I looked around and realized something: most of the people there weren’t in manufacturing.
They were in healthcare, education, service… even construction.
That’s when it hit me:
Lean thinking isn’t industry-specific.
It’s how smart businesses run—period.
Then I started working with civil contractors. Good people. Hard work. Big equipment. But no system. No structure. No simple way to run the business better, day by day.
Lean Dirt is the operating system made for the dirt world.
It’s simple. Practical. Easy to stick with.
Lean Dirt...
✅ Increases your production capacity
✅ Lowers your costs
✅ Gets everyone involved in making the business better
It’s daily maintenance for your business—just like your machines.
Lean Dirt makes it easier for your team to do the right work, the right way.
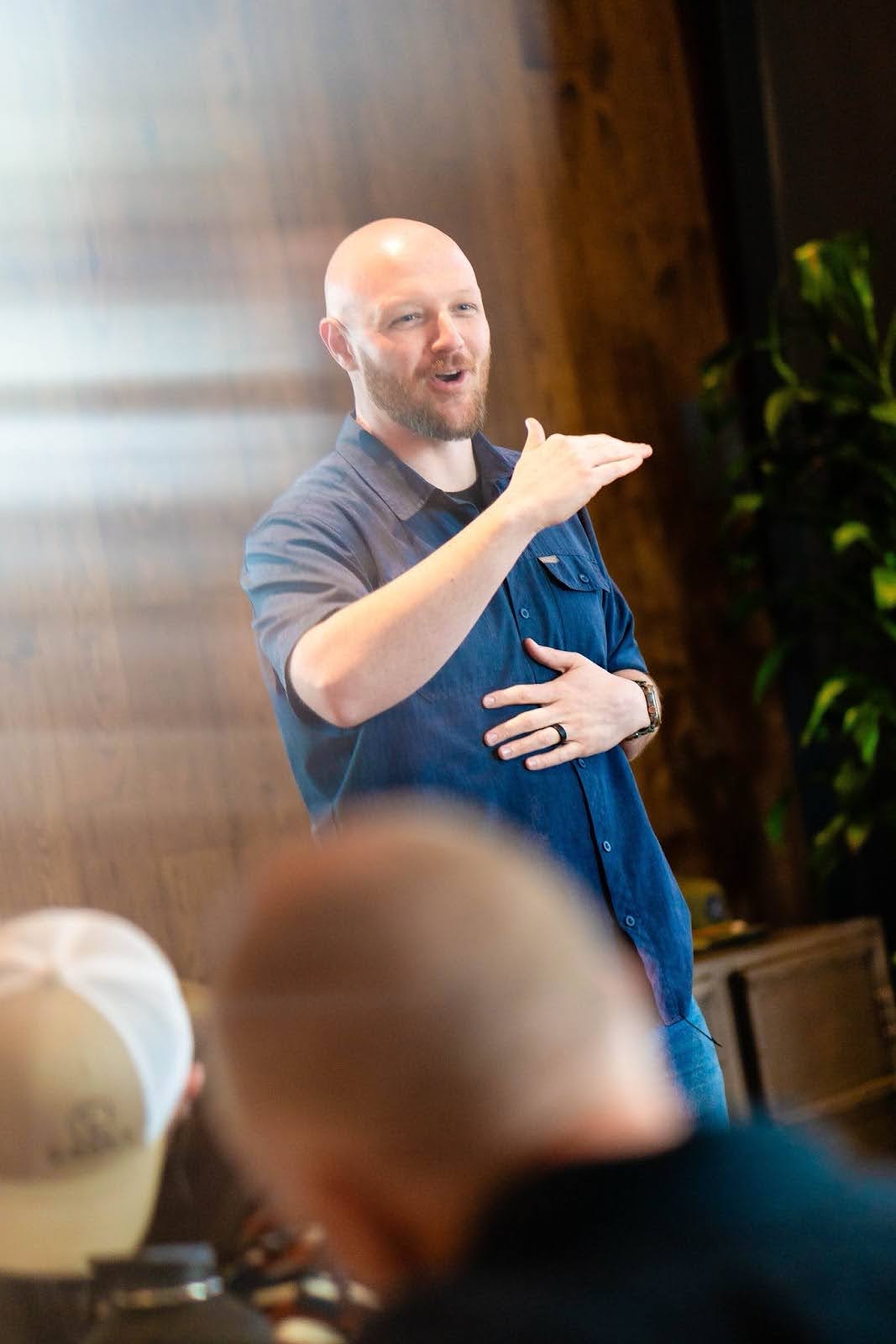
Tired of rework, delays, and chaos on the job?
- Clarity on where your business is stuck.
- Straight answers about building a team that improves daily.
- A practical next step to start building a business that runs lean.
See if
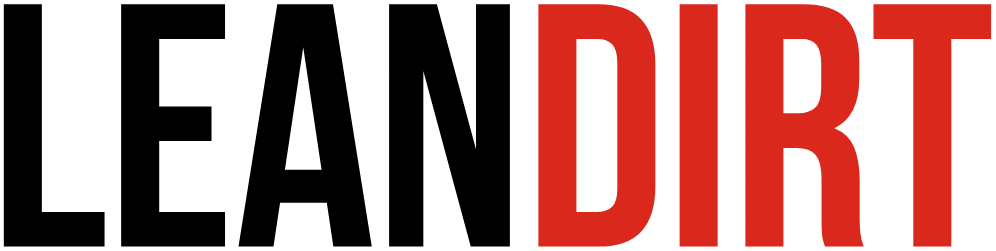